In this stage of the project, one of the main focuses is the development of a Decision Support System (DSS), led by TWI Hellas. This DSS outputs suggestions for rectification action to the prosthetist, aiming to improve the fitness of transfemoral prosthetic socket design. To accomplish this, we employ fuzzy-logic and rectification state-of-the-art algorithms that are baked in the DSS. These algorithms take as input the pressure measurements from sensors embedded in the prosthesis socket and use a set of fuzzy rules which encapsulate the prosthetist’s knowledge for deciding rectification actions, i.e. specific socket shape modifications to redistribute the pressures on the stump and lead to a better fitting of the socket (see Figure 1).
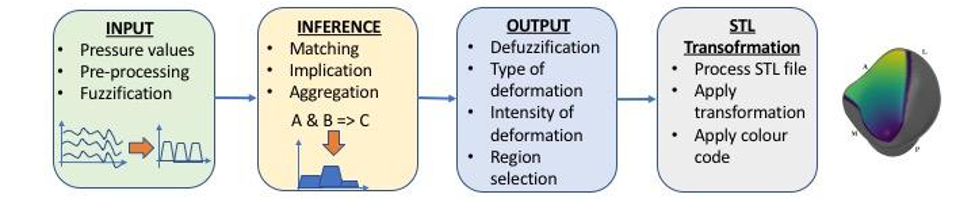
Τhe rules formulate the relationship between the evaluations of the prosthetist with their corresponding rectification actions and are described in a fuzzy manner using linguistic variables. These variables use labelled fuzzy sets (e.g. the variable “pressure” could be described as “Low”, “Medium”, “High” or “Very High” fuzzy sets). The rectification actions are then used to manipulate and modify a 3D digital socket model. These actions seek to increase the socket’s inner walls’ thickness on the anterior and lateral front (see Figure 2).
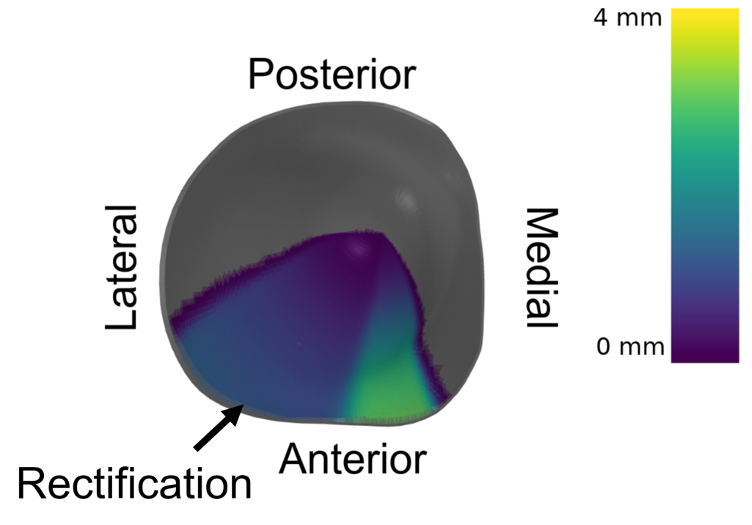
Finally, to validate the rectification actions of our DSS, we test its output in a Finite Element Analysis (FEA) simulation environment which replicates the process of donning and provides the pressure distribution on the stump. The simulation setup is led by KTH.
For validation purposes, we use three different sockets. One is the Nominal socket which we consider as a benchmark of a comfortable socket. This socket interfaces well with the stump, i.e. the pressure is evenly distributed in its inner surface and no high pressure is experienced in the femoral relief. The second is the Loose socket that is constructed from the Nominal by increasing its cross-sectional area by 5%. We consider this to be a socket with poor fitness, since the stump slides towards the distal end with no resistance, thus allowing high pressures to be experienced at the distal end. The third is the rectified socket, which is produced by our DSS. They are based on the Loose socket and seek to limit the high-pressure phenomenon at the distal end. All three types of sockets are simulated and compared with each other in Figure 3. In Figure 3(a) we observe the donning process of the Loose socket, where the stump is sliding towards the distal end and high pressures are experienced. Figure 3(b) and Figure 3(c), depict the simulation results of the donning process of a Nominal and a rectified socket. In these simulations, we observe that the stump doesn’t reach the distal end, and mild pressures are experienced on the lateral walls.
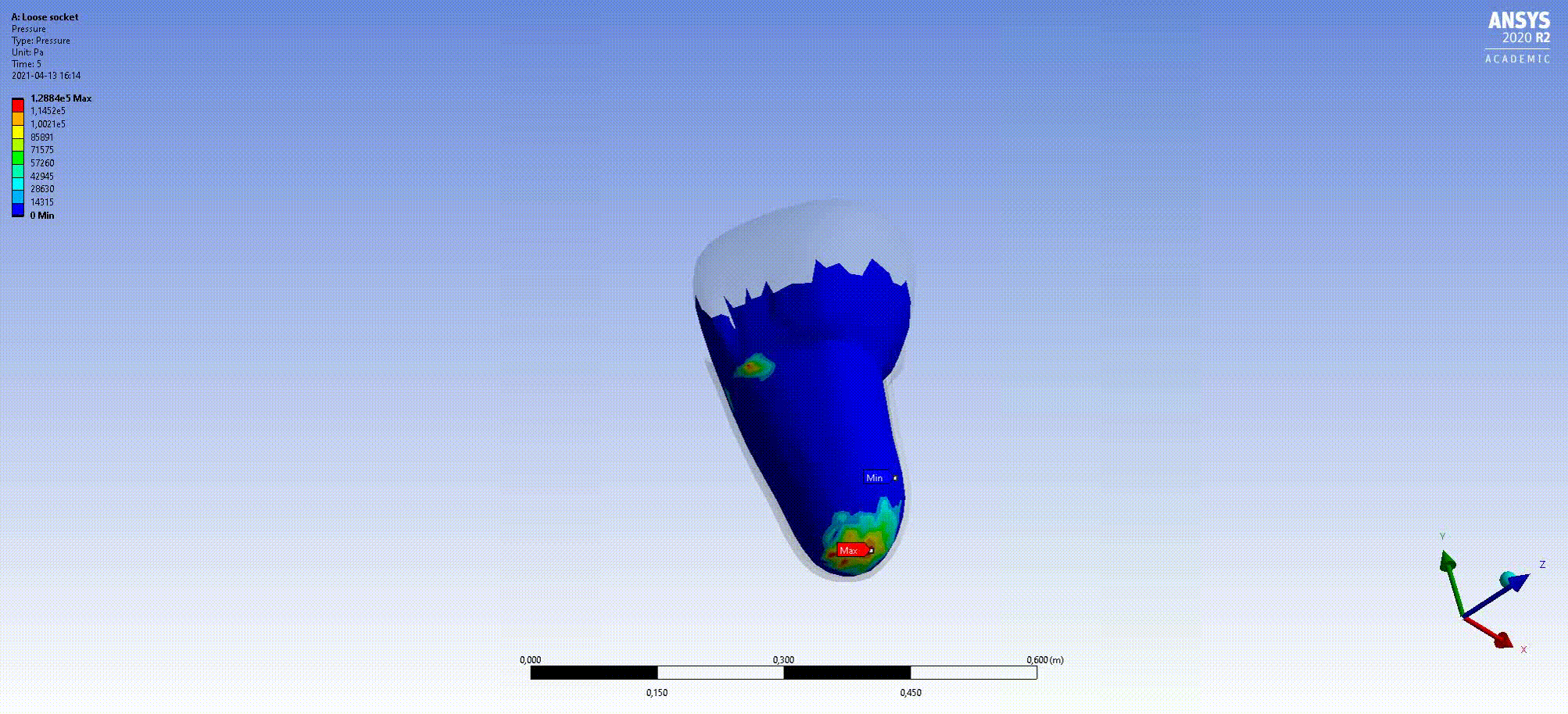
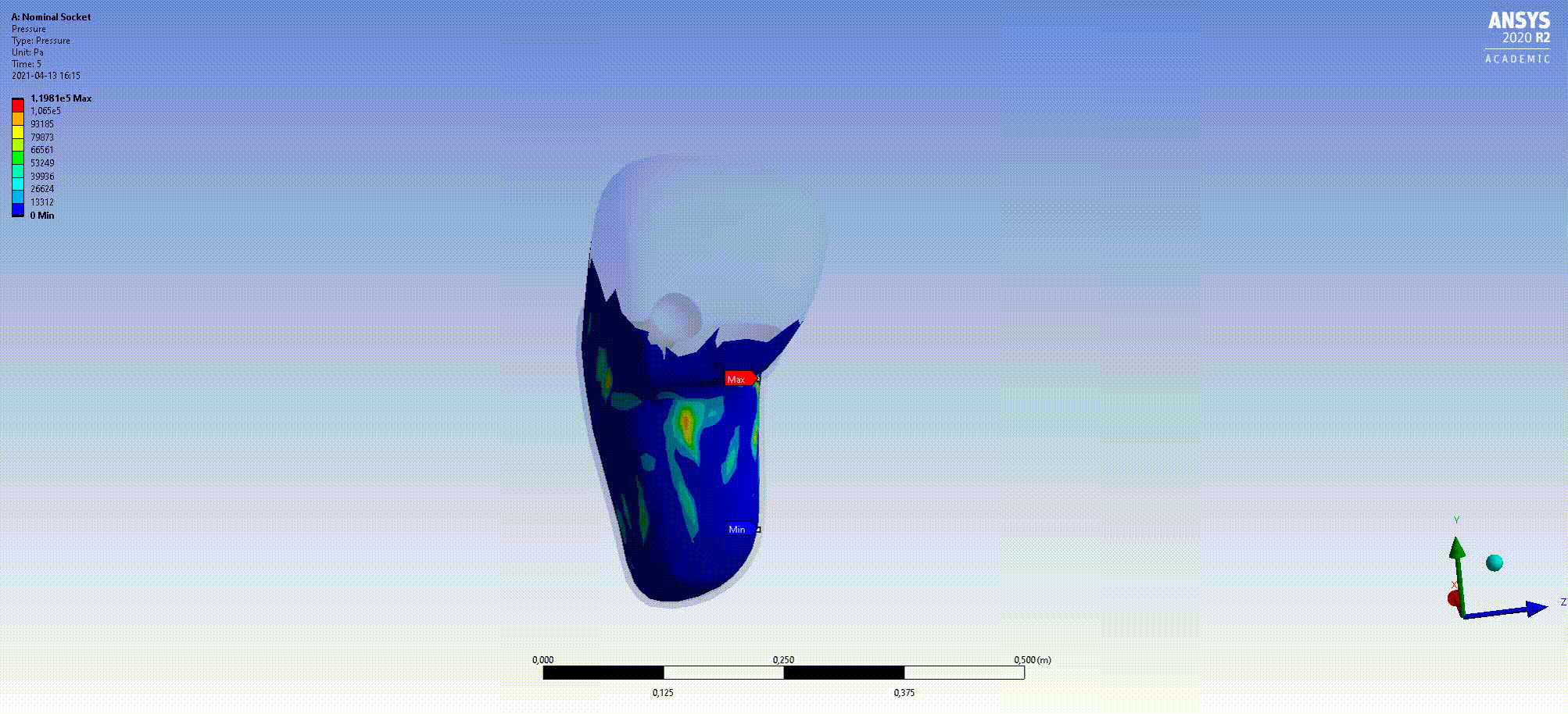
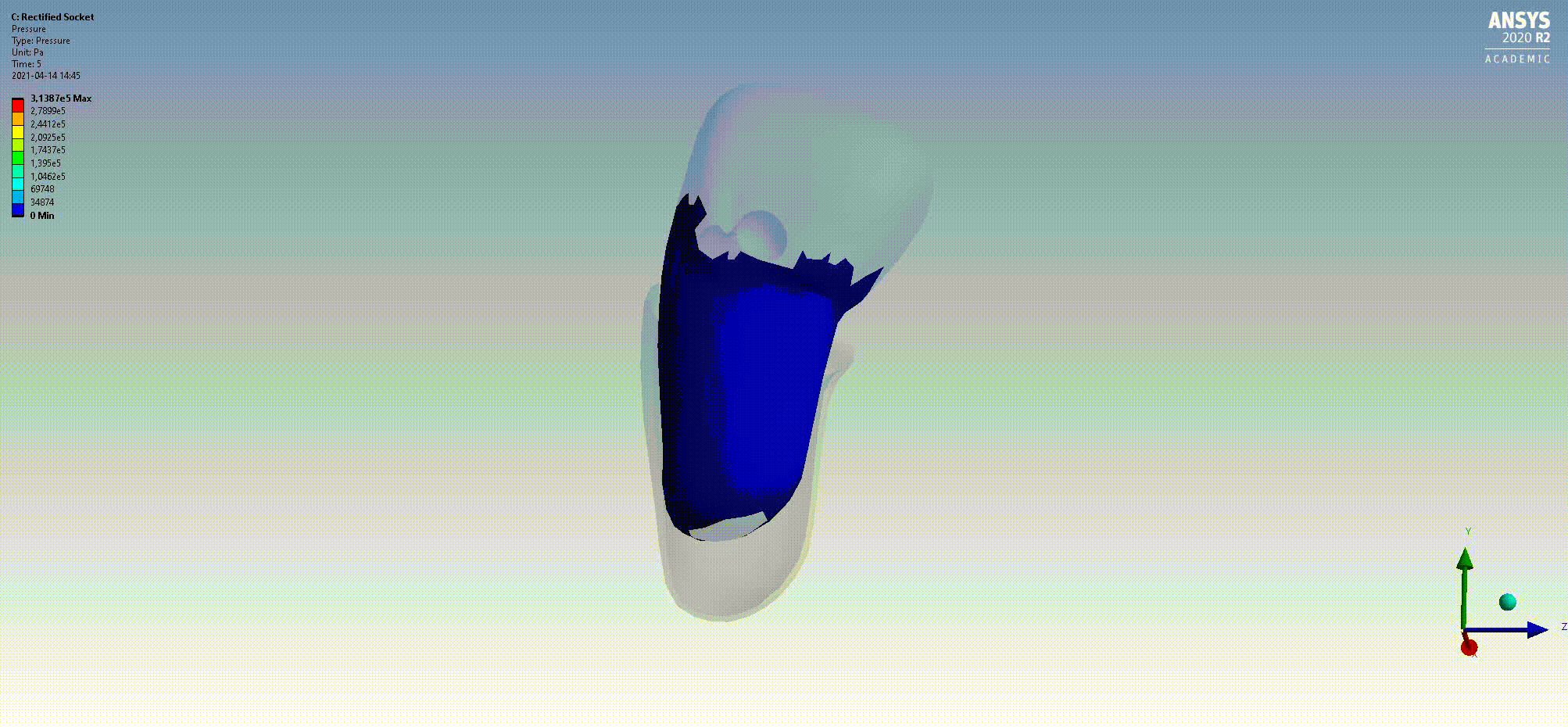